The MB15 alloy can be subjected to direct aging after extrusion or forging (T1) or an artificial aging process (T6). The strengths of these two heat treatments are approximately the same, but the plasticity of the latter is much lower. Generally, the T1 treatment is preferred. The solution treatment temperature of the MB15 alloy is relatively high (Ts = 500 – 525℃), which makes the grains grow easily and reduces plasticity. Conversely, direct artificial aging at 150 – 170℃ (T1) can avoid this drawback. Additionally, the hot working temperature of the MB15 alloy is 300 – 400℃. At this temperature, the strengthening phase is mostly dissolved, and air cooling can achieve a relatively high degree of supersaturation. Coupled with the grain refinement and increased recrystallization temperature effect of Zr, the extruded rods or profiles at this temperature have extremely fine grains, and after artificial aging, they can achieve high comprehensive performance.

Mechanical properties stipulated in the technical conditions of MB15 alloy
I. Chemical properties of MB15 alloy

II. Physical Properties of MB15 Alloy
In general corrosive media, MB15 alloy exhibits good corrosion resistance and shows no tendency for stress corrosion cracking. Surface oxidation treatment and oil or paint coating protection for MB15 alloy can be carried out following the regime for MB8 alloy.

Physical properties of MB15 alloy

Mechanical properties of MB15 alloy at room temperature (20℃)

Low-temperature mechanical properties of MB15 alloy extruded sheet

High-temperature mechanical properties of MB15 alloy
III. Process performance of MB15 alloy
The smelting and casting process of Mg-Zn-Zr alloy (MB15) is relatively complex. Due to the low solubility of zirconium in liquid magnesium, it is difficult to add, and zirconium has a high melting point (1860℃) and a density greater than that of magnesium, which easily leads to segregation. In addition, zirconium is chemically active and tends to combine with other elements in magnesium (mainly impurities) to form high-melting-point compounds that sink to the bottom of the crucible, resulting in significant loss of zirconium and often failing to meet the required zirconium content in the alloy, thereby reducing its grain refinement effect. Currently, zirconium is mostly added in the form of Mg-Zr master alloy or potassium zirconium fluoride (K2ZrF6).
Mg-Zn-Zr alloy has high plasticity within the hot working temperature range (300~450℃) and can be extruded into various specifications of bars, profiles, and strips. The alloy has good forging performance and can be used to manufacture large and complex-shaped forgings. The mechanical properties of MB15 alloy products obtained from a single extrusion of small-diameter ingots are higher than those of products obtained from double extrusion.

The main process parameters of MB15 alloy
IV. Applications of MB15 Alloy
MB15 alloy is mainly used in the production of bars, profiles, forgings and die forgings, and is suitable for manufacturing parts that need to withstand high loads and have high yield strength. The working temperature of the parts should not exceed 150℃.
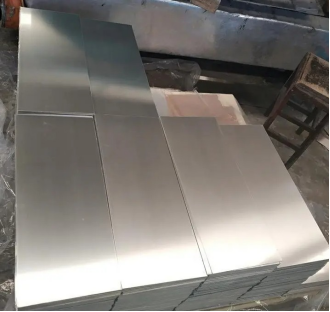
发表回复